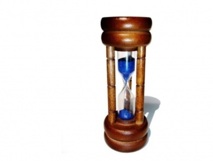
L’acronyme SMED se développe en Single Minute Exchange of Die, une formule que l’on pourrait traduire par changement rapide d’outil. Cette méthode consiste à optimiser le facteur temps de toute modification intervenant sur une chaîne de production de façon réduire au maximum sont immobilisation et donc sont coût. Grâce au SMED, Toyota a élaboré des processus qui lui ont permis de réduire le temps nécessaire à changer les outils de ses machines de quelques heures à quelques minutes.
Cette méthode est par ailleurs applicable à de nombreux procédés productifs, et procède de quelques étapes incontournables. Le secret du SMED est de faire la distinction entre les opérations qui requièrent impérativement un arrêt de production – désignées comme des « réglages internes » – et celles qui peuvent avoir lieu pendant la production – soit les « réglages externes » –. Le SMED propose donc, pour chaque processus de changement d’outil, d’établir une liste de ces opérations. Dans un premier temps, il sera nécessaire d’optimiser l’enchainement de ces différents réglages. Ensuite, la méthode SMED implique d’identifier tous les réglages internes qui pourraient être transformés en réglages externes. Il s’agira en dernier lieu de combiner le résultat de ces différentes étapes au sein d’un nouveau process de production plus efficace et économe en temps.
L’objectif du SMED est simple : permettre de fabriquer des pièces uniques sans occasionner d’augmentation de coûts. Un atout qui, s’il est obtenu, peut trouver de nombreuses applications. Le SMED en effet peut ainsi constituer la méthode de référence pour répondre à une demande spécifique émanant d’un client dont le cahier des charges serait original. Cette méthode peut donc être considérée comme un facteur d’agilité pour l’entreprise.
En tant que méthode d’optimisation des processus industriels, les applications du SMED sont multiples : on envisage en effet aisément son utilité pour faciliter le changement d’un tirage sur un circuit d’impression, pour remplacer un colorant sur une chaîne de teinture vêtement ou encore substituer un produit à un autre sur une ligne de conditionnement. Mes les origines industrielles du SMED ne doivent pas faire oublier son potentiel dans le cadre de processus manuels ou intellectuels. En effet, le SMED est un outil polyvalent et son usage résolument multisectoriel : il est utilisé par nombreuses entreprises pour améliorer une prestation commerciale, réduire l’indisponibilité d’un service informatique à l’occasion d’une maintenance, ou encore optimiser la productivité de la cuisine d’un chef étoilé. Chaque entreprise peut espérer en retirer un avantage en prenant le temps de réfléchir à la façon dont le SMED pourrait être appliqué à ses processus les plus gourmands en temps.
Cette méthode est par ailleurs applicable à de nombreux procédés productifs, et procède de quelques étapes incontournables. Le secret du SMED est de faire la distinction entre les opérations qui requièrent impérativement un arrêt de production – désignées comme des « réglages internes » – et celles qui peuvent avoir lieu pendant la production – soit les « réglages externes » –. Le SMED propose donc, pour chaque processus de changement d’outil, d’établir une liste de ces opérations. Dans un premier temps, il sera nécessaire d’optimiser l’enchainement de ces différents réglages. Ensuite, la méthode SMED implique d’identifier tous les réglages internes qui pourraient être transformés en réglages externes. Il s’agira en dernier lieu de combiner le résultat de ces différentes étapes au sein d’un nouveau process de production plus efficace et économe en temps.
L’objectif du SMED est simple : permettre de fabriquer des pièces uniques sans occasionner d’augmentation de coûts. Un atout qui, s’il est obtenu, peut trouver de nombreuses applications. Le SMED en effet peut ainsi constituer la méthode de référence pour répondre à une demande spécifique émanant d’un client dont le cahier des charges serait original. Cette méthode peut donc être considérée comme un facteur d’agilité pour l’entreprise.
En tant que méthode d’optimisation des processus industriels, les applications du SMED sont multiples : on envisage en effet aisément son utilité pour faciliter le changement d’un tirage sur un circuit d’impression, pour remplacer un colorant sur une chaîne de teinture vêtement ou encore substituer un produit à un autre sur une ligne de conditionnement. Mes les origines industrielles du SMED ne doivent pas faire oublier son potentiel dans le cadre de processus manuels ou intellectuels. En effet, le SMED est un outil polyvalent et son usage résolument multisectoriel : il est utilisé par nombreuses entreprises pour améliorer une prestation commerciale, réduire l’indisponibilité d’un service informatique à l’occasion d’une maintenance, ou encore optimiser la productivité de la cuisine d’un chef étoilé. Chaque entreprise peut espérer en retirer un avantage en prenant le temps de réfléchir à la façon dont le SMED pourrait être appliqué à ses processus les plus gourmands en temps.